Mastering the Art of Vacuum Forming: A Guide to Start Crafting Your Own Kydex Holsters
- Larry Shepard
- 6 days ago
- 5 min read
NOTE: This guide provides an overview of the fundamental process for creating a Kydex holster. Please note that it does not specify tool sizes, types, or encompass all the detailed steps involved in holster fabrication. We are currently developing a comprehensive resource that will include a complete list of the tools we use daily, along with a step-by-step instructional process for crafting your own holster. This upcoming guide will feature tool specifications, detailed instructions, and additional information, including how to construct your own vacuum table, complete with parts and tool lists.
Crafting a Kydex holster using vacuum forming is an engaging project that combines creativity with practicality. Whether you're an experienced holster maker or just beginning, making your own holster can be a rewarding experience. Kydex, a durable thermoplastic, is the ideal choice for crafting holsters thanks to its strength and shape retention. This guide will take you step-by-step through the process, detailing the necessary tools and materials to create a professional-quality Kydex holster.
What is Kydex and Why Use It?
Kydex is a high-performance thermoplastic valued for its ruggedness and versatility in holster making. Its benefits include:
Enhanced Retention Properties: Kydex holds its shape, providing a snug fit for your firearm.
Durability: Unlike leather, Kydex is resistant to wear and moisture, ensuring longevity and reliability.
Low Maintenance: Kydex requires little upkeep, staying functional and looking good over time.
Professionals often choose Kydex for custom holsters, with over 90% of law enforcement agencies using polymer-based materials like Kydex for their gear. This statistic underscores Kydex’s reliability as a trusted material for holsters.
Essential Tools and Materials
Before you start crafting your holster, it is crucial to gather all the necessary tools and materials. A list of tools that will make crafting your holster easier is below:
Tools
Vacuum Forming Machine/Table: This is essential for shaping the Kydex to fit your mold.
Heat source: Use this to soften the Kydex before forming. We lean toward toaster ovens that are large enough for up to 12"x12" sheets of Kydex and have a convection option.
Utility Knife: Perfect for cutting Kydex to the right dimensions.
Drills, Drill Press and Drill Bits: Needed for creating holes for fasteners. A drill press is recommended for preparing your holster molds.
Sanding/Finishing Tools: To smooth edges and improve surface finish. We use Dremels, a 4" x 36" and a 1" x 30" belt sander and a Benchtop Polisher for these tasks.
Measuring Tape or Ruler: Vital for accurate measurements.
Fabric Pencil: For marking cut and finish points on the Kydex.
Work Surface: Ensure it is heat-resistant and safe for crafting
Drill Press: A drill press is not required, but highly recommended. Especially for mold preparation.

Materials
Vacuum Mold: Vacuum Mold: Choose the correct mold for the specific firearm/light combo.
Kydex Sheets: 12" x 12" Kydex sheets in .080" thickness are ideal for most handguns.
Screws: Necessary for retention and belt clips
Belt Clips: For secure attachment to your belt.
Preparing the Vacuum Mold
Preparing and drilling a vacuum mold for a gun holster involves several critical steps to ensure a precise and durable final product. This process requires careful planning and execution to avoid damage to the mold and ensure a good fit for the holster once you have successfully vacuum formed your Kydex.
Drill Bit Selection: Choose drill bits appropriate for the material the mold is made of and the intended size of the holes. Ensure the bit is sharp and won't wander.
Drill Press Safety: Use a drill press with a securely mounted mold. This will prevent the mold from shifting during the drilling process.
Hole Placement: Most mold manufacturers include drill indicator marks for things such as retention hardware and belt clip locations. Most do not pre-drill the mold for vacuum holes. Select the appropriate drill bit size and drill around the trigger and sight channels, as shown in the sample image below.
Drilling Process: Drill the holes slowly and steadily, applying even pressure. Avoid excessive force, which could damage the mold or drill bit. Ensure the drill bit is aligned correctly to avoid creating misaligned or off-center holes.
Cleanup: Thoroughly clean the drilled holes to remove any debris or residue.

Preparing the Kydex Sheet
We recommend beginning by measuring and cutting your Kydex sheet in to a 12" x 12" piece. This will allow for plenty of Kydex to cover the mold and allow the suction of the vacuum to form and pull the hot Kydex into the mold.
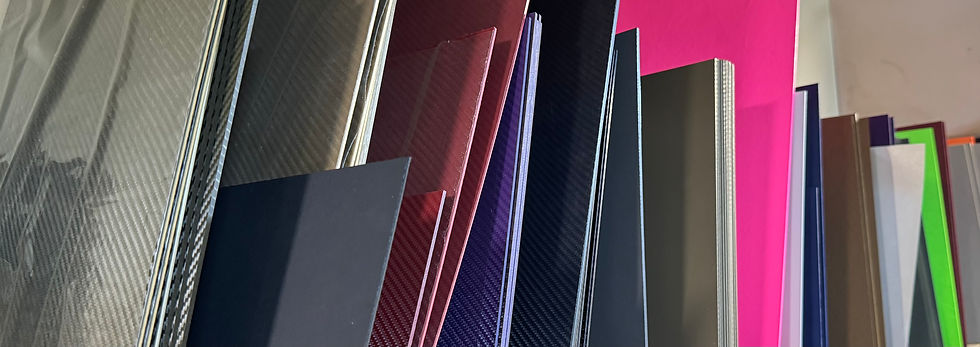
Heating the Kydex
Next, it’s time to heat the Kydex. Using your heat source, apply even heat across the Kydex. Ensure the Kydex becomes fully pliable without burning it (although this may vary per setup, we find that between 365-370 degrees fahrenheit is the best temperature range for vacuum forming), as overheating can damage the material. Aim for a flexible but firm state that will hold the mold’s contours.
Work quickly after heating; the Kydex will cool and harden fast, so proceed to the vacuum forming stage immediately.
Vacuum Forming Process
Position the heated Kydex sheet over your firearm mold on the vacuum forming machine/table. Activate the vacuum to pull the Kydex tightly over the mold. This process is crucial for achieving that customized fit. We use a 12 CFM vacuum pump on our vacuum table with a foot pedal so that both hands are available for handling the Kydex sheet.
Keep a close eye on the formation. Once the Kydex has cooled and set correctly (this can be sped up by using an air compressor and blowing air over the kydex), turn off the vacuum and carefully lift your new holster from the mold. Tapping the Kydex to break the mold loose may be necessary.

Cutting and Finishing Touches
Once the molded Kydex is out, cut the excess Kydex off as shown in above image. Cut out sight channel and round any rough corners with a Dremel. Smooth out sharp edges with buffer/polisher to ensure a comfortable fit when worn.
Drill holes for your fasteners, installing rivets or screws along with your belt clips or loops tailored to your carrying style.
Additional steps are necessary depending on the type of holster your are creating. Look for our future posts with detailed step by step processes for making different styles of vacuum formed holsters.
Final Assembly
After securing all components, ensure every part is securely attached, and assess the holster for fit and comfort. A well-designed holster should stay in place while providing easy access to your firearm.
Craft Your Own Holster with Confidence
Creating a Kydex holster through vacuum forming can be an enjoyable and satisfying project. By following this guide and utilizing the right tools and materials, you can design a customized, durable holster tailored to your needs.
Kydex holsters offer protection and security while allowing you to personalize their design. Whether you prefer a basic style or something more intricate, your creativity is the only limit.
Gather your tools and materials today, and embark on your crafting journey! Enjoy the process and happy crafting!
© 2025 IndyConcealment.com | All rights reserved.
Comments